DA-UB
In-Line Detonation Flame Arrester for unstable and stable detonations and deflagrations in a straight through design with a shock tube, bidirectional
- optimized performance due to the patented Shock Wave Guide Tube Effect (SWGTE)
- low number of FLAMEFILTER® discs due to the patented shock tube (SWGTE)
- modular design enables replacement of the individual FLAMEFILTER® discs
- different designs allow scalable pressure loss over the area of the FLAMEFILTER®
- maintenance-friendly design
- advanced design for higher operating temperatures and pressures
- bi-directional operation, as well as any flow direction and installation position
- installation of temperature sensors possible
- minimal pressure loss resulting in low operating and lifecycle costs
- cost-effective spare parts
Function and Description
The type PROTEGO® DA-UB in-line detonation flame arresters are the newest generation of flame arresters. Based on fluid dynamic and explosion-dynamic calculations, as well as decades of field tests, a line was developed that offers minimum pressure loss and maximum safety. The device uses the Shock Wave Guide Tube Effect (SWGTE) to separate the flame front and shock wave. The result is an in-line detonation flame arrester without a classic shock absorber, and the use of flame-extinguishing elements is minimized.
The devices are symmetrical and offer bi-directional flame arresting for deflagrations and stable and unstable detonations. The arrester essentially consists of two housing parts with an integrated shock tube (1) and the PROTEGO® flame arrester unit (2) in the center. The PROTEGO® flame arrester unit is modular and consists of several FLAMEFILTER® discs (3) and spacers firmly held in a FLAMEFILTER® casing. The number of FLAMEFILTER® discs and their gap size depends on the arrester’s intended use.
By specifying the operating conditions, such as the temperature, pressure, explosion group, and the composition of the fluid, the optimum detonation arrester can be selected from a series of approved devices. PROTEGO® DA-UB flame arresters are available for explosion groups IIA to IIB3 (NEC group D to C MESG ≥ 0.65 mm).
The standard design can be used at an operating temperature of up to +60°C / 140°F and an absolute operating pressure up to 1.1 bar / 15.9 psi. Devices with special approval for higher temperatures and pressures (see table 3) are available upon request.
EU conformity according to the currently valid ATEX directive. Approvals according to other national/international regulations on request.
Dimensions
To select nominal width/nominal size (NG/DN) - combination, please use the flow capacity charts on the following pages
Additional nominal width/nominal size (NG/DN) - combinations for improved flow capacity upon request
NG | 150 / 6" | 150 / 6" | 200 / 8" | 300 / 12" | 400 / 16" | 500 / 20" | 600 / 24" | 700 / 28" | 800 / 32" | 1400 / 56" | |
DN | ≤ 50 / 2" | 65, 80 / 2 ½“, 3 | ≤100 / 4" | ≤150 / 6" | ≤ 200 / 8" | ≤ 250 / 10" | ≤ 300 / 12" | ≤ 350 / 14" | ≤ 400 / 16" | ≤ 600 / 24" | |
a | 285 / 11.22 | 285 / 11.22 | 340 / 13.39 | 445 / 17.52 | 565 / 22.24 | 670 / 26.38 | 780 / 30.71 | 895 / 35.24 | 1015 / 39.96 | 1675 / 65.94 | |
b | IIA -P1,1 | 700 / 27.56 | 800 / 31.50 | 1000 / 39.37 | 1200 / 47.24 | 1400 / 55.12 | 2200 / 86.61 | ||||
IIA -P1,2 | 388 / 15.28 | 388 / 15.28 | 488 / 19.21 | 626 / 24.65 | |||||||
IIB3-P1,1 | 500 / 19.69 | 638 / 25.12 | 724 / 28.50 | 824 / 32.44 | 1000 / 39.37 | 1200 / 47.24 | 1400 / 55.12 | ||||
IIB3-P1,2 | 388 / 15.28 | 388 / 15.28 | |||||||||
c | 500 / 19.69 | 500 / 19.69 | 520 / 20.47 | 570 / 22.44 | 620 / 24.41 | 670 / 26.38 | 720 / 28.35 | 770 / 30.31 | 820 / 32.28 | 1060 / 41.73 |
Material selection for housing
Design | A | B | C |
Housing | Steel | Stainless Steel | Hastelloy |
Heating jacket (DA-UB-(T)-H-...) | Steel | Stainless Steel | Stainless Steel |
Gasket | PTFE | PTFE | PTFE |
Flame arrester unit | A | B, C | D |
Material combinations of flame arrester unit
Design | A | B | C | D |
FLAMEFILTER® cage | Steel | Stainless Steel | Stainless Steel | Hastelloy |
FLAMEFILTER®* | Stainless Steel | Stainless Steel | Hastelloy | Hastelloy |
Spacer | Stainless Steel | Stainless Steel | Hastelloy | Hastelloy |
Selection of explosion group
MESG | Expl. Gr. (IEC / CEN) | Gas Group (NEC) |
≥ 0,65 mm | IIB3 | C |
Selection of max. operating pressure
Expl. Gr. | DN | 50 / 2" | 80 / 3" | 100 / 4" | 150 / 6" | 200 / 8" | 250 / 10" | 300 / 12" | 350 / 14" | 400 / 16" | 600 / 24" |
NG | 150 / 6'' | 150 / 6'' | 200 / 8'' | 300 / 12'' | 400 / 16'' | 500 / 20'' | 600 / 24'' | 700 / 28'' | 800 / 32'' | 1400 / 56'' | |
IIA | Pmax | 1,8 / 26.1 | 1,8 / 26.1 | 1,6 / 23.2 | 1,6 / 23.2 | 1,1 / 15.9 | 1,1 / 15.9 | 1,1b / 15.9 | 1,1 / 15.9 | 1,1 / 15.9 | 1,6 / 23.2 |
IIB3 | Pmax | 1,5 / 21.7 | 1,5 / 21.7 | 1,5 / 21.7 | 1,5 / 21.7 | 1,1 / 15.9 | 1,1 / 15.9 | 1,1 / 15.9 | 1,1 / 15.9 | 1,1 / 15.9 |
Specification of max. operating temperature
≤ 60°C / 140°F | Tmaximum allowable operating temperature in °C |
- | Designation |
Flange connection type
EN 1092-1; Form B1 |
ASME B16.5 CL 150 R.F. |
Design Types and Specifications
There are four different designs available:
Basic design of the detonation arrester | DA-UB- – - – |
In-line detonation flame arrester with integrated temperature sensor* as additional protection against short time burning | DA-UB- T - – |
Detonation arrester with two integrated temperature sensors* as additional protection against short time burning from both sides | DA-UB- TB - – |
In-line detonation flame arrester with heating jacket | DA-UB- H - |
Additional special arresters upon request
*Resistance thermometer for device group II, category (1) 2 (GII cat. (1) 2)
Flow Capacity Chart
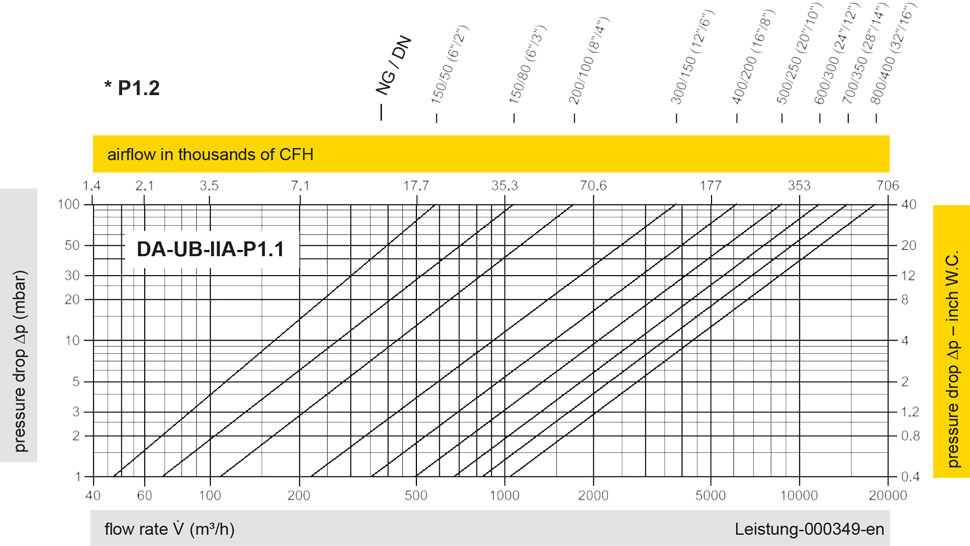
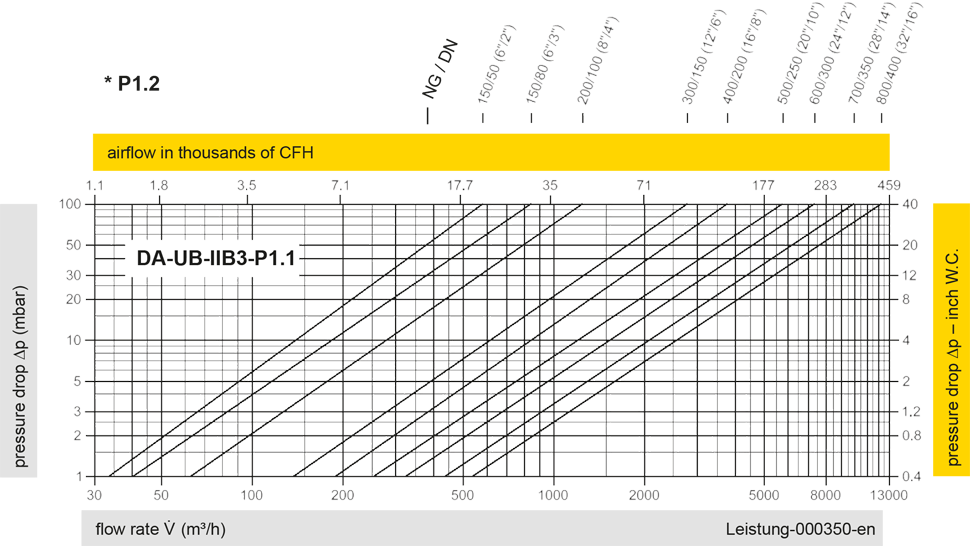
The flow capacity charts have been determined with a calibrated and TÜV certified flow capacity test rig. Volume flow V in (m³/h) and CFH refer to the standard reference conditions of air ISO 6358 (20°C, 1bar). For conversion to other densities and temperatures refer to Sec. 1: “Technical Fundamentals”.
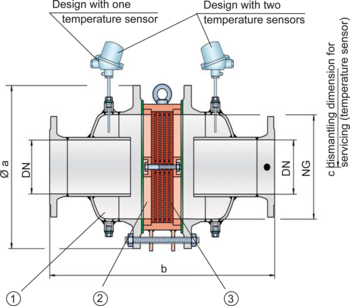
