Function and Description
PROTEGO® air-drying device of types LA or LA/V is used when suction air must be dried for atmospheric venting of storage tanks where only little or no humidity is allowed to get into the tank or the stored product due to the process engineering. They are usually used in vertical or horizontal aboveground tanks which store non-flammable or flammable liquids, and which must not be vented with humid air for safe operation.
The single device PROTEGO® LA mainly consists of the drying agent container (1). Its snap closing elements (2) connect it to the connection head (3) with flange connection according to DIN 2501 or to any other international standard.
The bottom screen (4) and the protective strainer (5) are firmly welded into the drying agent container (1). The upper strainer cover (6) is loose. It can be removed easily to add or remove the drying agent. The connection head (3) contains the sealing plate (7) that closes the connection head opening when taking the drying agent container off. No humid air can be sucked in when changing the drying agent container.
The upper part of the drying agent container (1) holds the integrated control cartridge (8). The control cartridge can be removed during operation. It shows if the drying agent contains humidity and has to be replaced for regeneration.
Depending on the required flow rates or prescribed pressure losses the drying agent containers are delivered in two sizes – type I or type II. As parts of a modular system they are assembled into larger performance units.
KC® drying pearls are used as the drying agent. The control cartridge (figure 1) is filled with special KC® indicator drying pearls. The required filling levels are specified in the relevant operating instructions.
The air-drying device type LA/V is essentially similar to type LA. Additionally, it has a replaceable check valve (9) with protective strainer and valve pallet (10) integrated in the inlet connection. When no air is sucked in through the air-drying device the device is sealed and tight towards the atmosphere. So at high air humidity the drying agent in the lower area of the drying agent container cannot absorb moisture.
The FEP diaphragm with air cushion sealing (figure 2) is used as valve pallet sealing up to pressure range II. From pressure range III, a lapped metallic sealing is used (figure 3). Air-drying devices of types LA or LA/V may be integrated into complete tank venting systems (see figures 4 and 5).
If flammable liquids are stored in the tank, then flame arresters have to be installed in addition to the air-drying device and the pressure and vacuum relief valves. Depending on the operating conditions it is also possible to combine other vent valves with the integrated air-drying device.
When the set vacuum is reached in the tank, the vacuum relief valve – for instance PROTEGO® type DZ/T or DV/ZU on figures 4 and 5 – connected to the air-drying device opens and the drying device LA sucks in atmospheric air while the drying agent (KC® drying pearls) absorbs the atmospheric humidity.
The drying agent must be replaced and regenerated when depleted. Using a control cartridge, it is easily possible to determine whether the drying agent is saturated with humidity.
If the specified pressure is reached in the examples shown in figures 4 or 5 the pressure side of the combined pressure and vacuum relief valve opens and the product vapour/air mixture escapes into the atmosphere. The valve could be for instance PROTEGO® type VD/SV or DV/ZU. Alternatively it is possible to pass the product vapour/air mixture through a suitable valve – e.g. PROTEGO® type DV/ZU into an exhaust line or exhaust system. Under pressure the vacuum side of the above valves remains closed and the product vapours cannot pass into the drying agent.
In larger tanks it is recommended to also use combined pressure and vacuum relief valves e.g. PROTEGO® type VD/SV. This ensures that in an emergency (failure of air-drying device) atmospheric air can be sucked in directly through the vacuum side. Often direct atmospheric emergency venting is required yet it is neither possible nor necessary to size the air-drying device for the maximum volume flow calculated (pump flow-rate and thermal flow according to EN 14015 or API 2000). Maximum thermal flow occurs only rarely and it is therefore usually sufficient to size the air-drying device according to the pump flow-rate for emptying and a thermal flow portion of approximately 25%.
Essentially, the air-drying device type PROTEGO® LA/V functions like type PROTEGO® LA. However, a check valve allows inbreathing only when the entire venting system – the tank and the drying container – is under vacuum at the set pressure of the check valve.
The devices are designed for venting rates sufficient for the breathing of storage tanks. However, they do not replace any valves designed for emergency venting.
The drying agent saturation can be easily monitored using a control cartridge. The drying agent can be regenerated. Drying agent and control drying pearls are not included in the PROTEGO® LA or LA/V and can optionally be ordered together with the device.
Figure 6 shows the combination options of PROTEGO® LA/V air-drying device in complete units. The overall dimensions, filling volumes and filling weights are also given in this figure.
Material selection Typ LA
Design | A | B | |
Housing | Steel | Stainless Steel | |
Bottom screen | Stainless Steel | Stainless Steel | |
Protective strainer | Stainless Steel | Stainless Steel | |
Cover | Steel | Stainless Steel |
Material selection Typ LA/V
Design | A | B |
Housing | Steel | Stainless Steel |
Bottom screen | Steel | Stainless Steel |
Protective strainer | Stainless Steel | Stainless Steel |
Cover | Steel | Stainless Steel |
Valve insert | Stainless Steel | Stainless Steel |
Material selection for vacuum relief valve
Design | A | B | C |
Vacuum range [mbar] [inch W.C.] | -3.5 up to -5.0 -1.4 up to -2.0 | ≥-5.0 up to -14 ≥-1.4 up to -5.6 | ≥-14 up to -35 ≥-5.6 up to -14 |
Valve pallet | Aluminium | Stainless Steel | Stainless Steel |
Sealing | FEP | FEP | Metal to Metal |
Data Necessary for Specification
Maximum allowable tank vacuum pT (mbar or Inch W.C.)
Maximum possible volume flow V (m3/h or CFH) (when emptying the tank)
Pressure loss or Pipeline length
Tank material
Selection and Design
In a system shown in figure 4 the maximum vacuum in the tank is calculated depending on the volume flow of the pressure loss ∆pLA of the air drying-device LA and the opening pressure pO of the vent valve DZ/T or DV/ZU or the tank pressure pT given in the relevant capacity chart.
In a system according to figure 5 the maximum vacuum in the tank is calculated depending on the volume flow of the pressure loss ∆pLA of the air-drying device LA - plus check valve set pressure pVR - and opening pressure pO of the vent vent valve DZ/T or DV/ZU or the tank pressure pT given in the relevant capacity chart.
Additionally, the pressure loss in the pipeline between air-drying device and vent valve has to be taken into account; however, usually it is negligible.
Flange connection type
The connection flange is to EN 1092-1 or DIN 2501, PN 16. Optionally, the connecting flange can be made according to any international flange standard.
Design Types and Specifications
There are two designs available:
Air-drying device, basic design | LA |
Air-drying device with check valve | LA/V |
Flow Capacity Chart
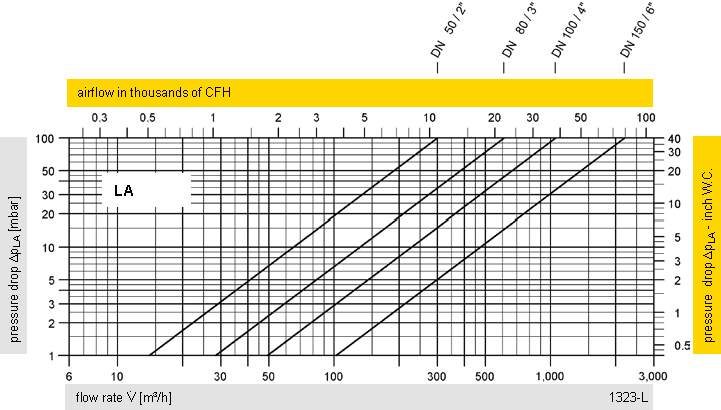
The stated capacities are valid for the single device PROTEGO® LA and refer to the filling material KC® dryer pearls of 2 up to 5 mm Diameter. The totel pressure drop of typ PROTEGO® LA/V is ∆pLA/V results from the differential pressure ∆pLA/V plus adjusted Setting of vacuum valve pVR.
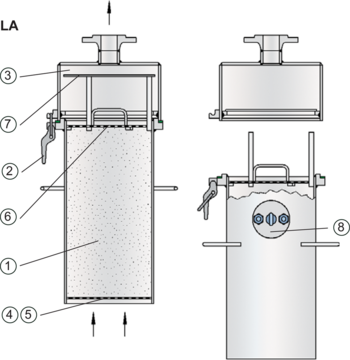
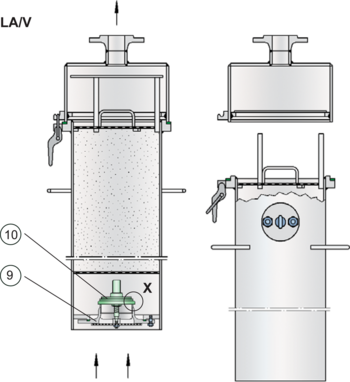

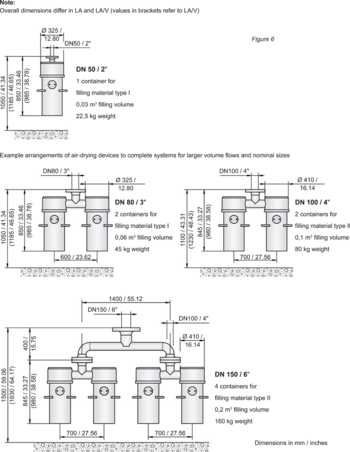
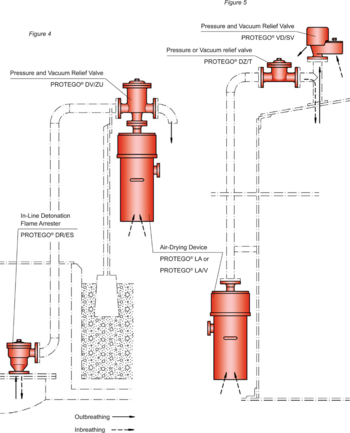
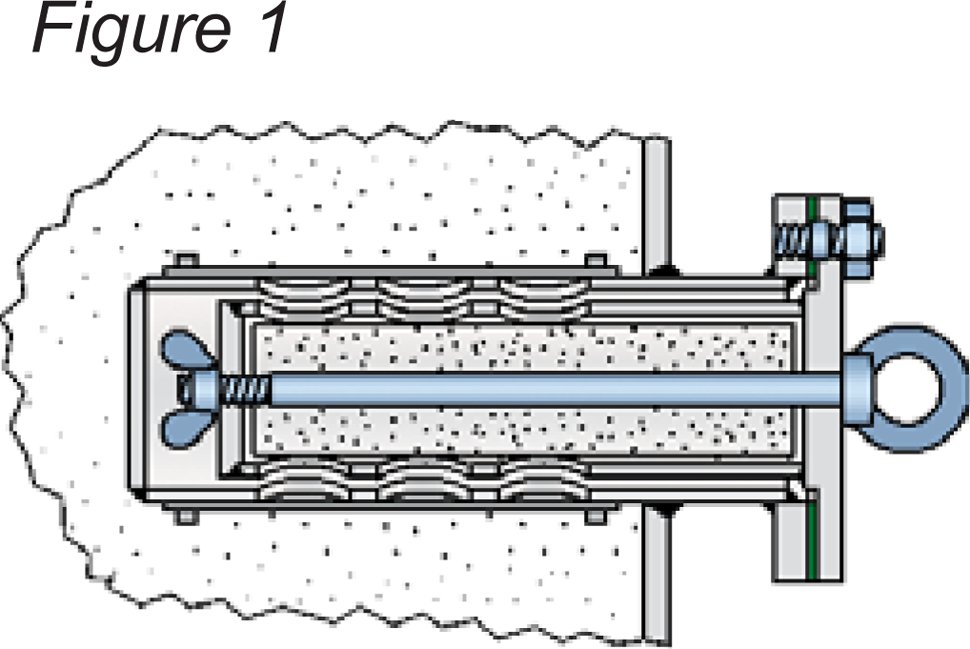